No. 1,053,274 – Plane (James M. Burdick And Christian Bodmer) (1913)
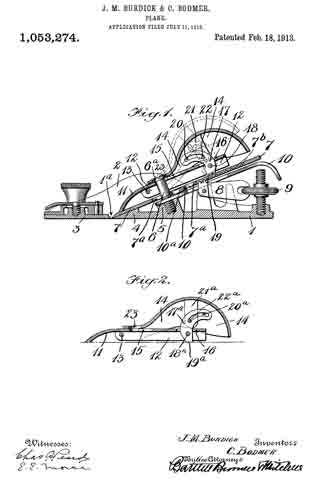
UNITED STATES PATENT OFFICE.
_________________
JAMES M. BURDICK AND CHRISTIAN BODMER, OF NEW BRITAIN, CONNECTICUT, ASSIGNORS TO THE
STANLEY RULE & LEVEL COMPANY, OF NEW BRITAIN, CONNECTICUT, A CORPORATION OF CONNECTICUT.
PLANE.
_________________
1,053,274. Specification of Letters Patent. Patented feb. 21, 1913.
Application filed July 11, 1912. Serial No. 708,762.
_________________
To all whom it may concern:
Be it known that we, JAMES M. BURDICK and CHRISTIAN BODMER, citizens of the United States, residing at New Britain, Hartford county, State of Connecticut, respectively, have invented certain new and useful Improvements in Planes, of which the following is a full, clear, and exact description.
This invention relates to an improvement in the construction of planes, and is more particularly concerned with the construction of a detachable cap piece for the cutter or “plane iron”. In such cap pieces, it has hitherto been the practice to provide a detachable cap piece provided with means for engaging with the cutter and clamping it in position upon its seat upon the plane body.
Our invention contemplates employing such a cap piece and utilizing one of the parts thereof as a palm rest. More specifically, the invention contemplates the employement of a base plate adapted to be seated over the cutter and a relatively movable palm rest portion, the cutter clamping means being carried by said cap piece and placed in clamping position by the movement of the palm rest relative to the base plate when the cap is seated on the plane over the cutter. In such a construction the locking parts are housed within the palm rest portion of the cap and thereby protected against accidental displacement. Furthermore, the cap is locked against loosening movement on the plane after the parts have once been moved to clamping position. Such a construction is shown and broadly claimed in our co-pending application Serial No. 708,733.
Our present invention comprises a new specific embodiment of the broad combinations of structure contained in said co-pending application and comprises more especially the specific combinations of parts recited in detail in the following specification and illustrated in the accompanying drawings.
In the drawings: Figure 1 is a longitudinal sectional view through a standard type of plane equipped with a detachable cap constructed in accordance with the present invention. Fig. 2 is a longitudinal section through a modified form of cap detached from the plane body.
Referring to the drawings by numerals: 1 designates the body of a plane provided with side walls or flanges 2 and a detachable shoe 3 at the forward end thereof, a throat 1a being formed at the forward end of the plane and in the rear of the detachable shoe portion thereof. 4 designates a frog or seat for the forward end of the “plane iron” or cutter, and 5 an interiorly threaded boss projecting upwardly from the plane body and carrying what is commonly termed a “cap screw” 6 provided with the usual headed end 6a. An adjusting lever 10 has its forward end seated over the boss 5 and is provided with an adjusting head 10a. To the rear of said head is a second adjusting device comprising a lever member 8 plvotally mounted at its forward end in the plane body and engaged at its rear end by an adjusting nut 9. A “plane iron” or cutter 7 is seated on the body of the plane with its forward end resting upon the frog or seat A and its cutting edge projecting into the throat 1a, the intermediate portions of the cutter resting respectively over the forward ends of the adjusting lever 10 and of the second adjusting lever 8. This cutter is provided with the usual longitudinal slot 7a through which the cap screw 6 projects and through and within which the adjusting head 10a extends, and with a plurality of corrugations 7b formed in its under face which are engaged by the forward end of the adjusting lever 8 to effect vertical adjustment of the cutting edge of the cutter. The lever 10, through its adjusting head 10a, effects lateral or angular adjustment of said cutting edge.
The parts so far described are merely those of a standard type of plane which has been selected for the illustrative application of the detachable cap embodying our invention. This cap embodies a base plate 11 having its forward end beveled and adapted for engagement with the forward end of the cutter 7, and is provided with the side walls or flanges 12. A pivot pin 13 extends transversely of the base plate 11 through the side walls 12 thereof, and has pivotally mounted upon its ends the forward ends of a palm rest section 14 the rear portion of which is formed as a hollow convex body serving as a palm rest. The body of the base plate adjacent the location of the forward end of the palm rest section is provided with a key-hole slot 15, and rearwardly thereof and adjacent the end of the base plate, with a second slot 16 through which extends the lower end of a lever member 17 pivotally carried by said base plate by means of the pivot pin 18 extending transversely of the base plate between the side walls 12 thereof. The lower edge of this lever is formed as a cam 19 and its upper end is formed with a curved oifset provided with a curved slot 20 therein. Projecting downwardly from the interior face of the palm rest 14 is an arm or bracket 21 provided with a pin 22 fitting within the curved slot 20 and designed, when the palm rest section is moved relative to the base plate, to cooperate with said slot and the upper end of said lever to move the lower cam end of the lever toward and away from the upper face of the cutter 7, or, when a clamping plate is employed in connection with said cutter, toward and away from said clamping plate. The forward end of the palm rest section of the cap in alinement with the forward edge of the keyhole slot 15 of the base plate, is provided with an aperture 23 designed to lit over the head 6a of the cap screw when the palm rest is moved downwardly, the sides of the palm rest adjacent said aperture forming an annular shoulder engaging the abutment formed by the head of said cap screw.
In Fig. 2, the cap shown therein is provided with the base plate 11, side walls or flanges 12, pivot pin 13, palm rest 14 pivotally carried thereby, keyhole slot 15, a second slot 16 to the rear of said keyhole slot and adjacent the rear of the base plate, and with an aperture 23 in alinement with the forward edge of the keyhole slot, these parts being the same as those shown and described in connection with Fig. 1. The lever member 17a, however, which is pivotally mounted in the base plate by means of the pivot pin 18a and has its lower end formed as a cam 19a is provided with a rearwardly extending offset instead of the forwardly extending curved offset shown in Fig. 1. This rearwardly extending offset is provided with a curved slot 20a and an arm or bracket 21a extending downwardly from the inner face of the palm rest section 14 and carries a pin 22a engaging in and cooperating with the curved slot 20a and the upper end of the lever member 17a’ to move the lower cam end 19a of the lever into and out of clamping engagement with the face of the cutter 7.
The application and operation of both forms of cap is substantially the same, and is as follows: Assuming that the cutter 7 is seated on the plane body and its parts, as is shown in Fig. 1, the detachable cap is seated over said cutter by bringing the enlarged end of the keyhole slot 15 in its base plate 11 over the head of the cap screw 6 and then moving the base plate and its attached palm rest section upwardly on the cutter to bring the narrow portion of the keyhole slot under the head 6a of the cap screw. When this is being done, the palm rest section of the cap is in raised position, as indicated in dotted lines in Fig. 1 of the drawings. After the base plate has been engaged with the cutter and cap screw 6, as described, the palm rest section is swung downwardly relatively to the base plate, this movement, through pins 22–22a, swinging the lower cam edges 19–19a of the clamping levers into frictional clamping engagement with the upper face of the cutter 7 so that by the time the pins 22–22a reach the lower ends of slots 20–20a to stop the further relative movement between the palm rest and base plate, the cam ends 19–19a will have frictionally engaged and securely clamped the cutter 7 in position on the plane body. This clamping engagement is such that it holds the cutter so tightly on its seat that under ordinary service conditions, its position relative to the plane body will remain unchanged. The cutter, however, is always capable of being adjusted without in any way loosening the cap.
Owing to the engagement of the keyhole slot 15 with the cap screw 6, there is a possibility that during service the cap might be loosened and slide longitudinally of the cutter 7 despite the fact that its bottom plate is held to said cutter by the frictional engagement therewith of its clamping lever. The provision of the apertures 23 in the forward end of the palm rest section is designed to prevent any possibility of such movement, and when the palm rest is moved downwardly to actuate the clamping lever to frictional clamping engagement with the cutter, the head 6a of the cap screw projects through this aperture 23, the edges of the palm rest section adjacent said aperture forming annular shoulders engaging the abutment formed by the head of the cap screw and preventing movement of the cap relative to the plane body.
To detach the cap from the plane, it is only necessary to move the palm rest upwardly from the base plate, the application of sufiicient force causing the pin 22 or 22a to move in the curved slot of the clamping lever member and by frictional pressure, move the lower cam end of the lever out of clamping engagement with the cutter 7. When the palm rest has thus been moved upwardly and the cam end of the lever retracted from engagement with the cutter, the forward apertured end of this palm rest section will have been moved from locking engagement with the head of the cap screw, and the base plate 11 may now be moved downwardly on the cutter 7 to bring the enlarged end of the keyhole slot in line with the cap screw 6, whereupon the base plate and its attached palm rest may be removed from the cutter and plane body.
The structure of the cap and its connections is susceptible of modification within the spirit of our invention and the scope of the appended claims.
What we claim, therefore, and desire to secure by Letters Patent is:
1. In a plane, in combination, a body provided with a cutter seat, a cutter positioned thereon, an abutment carried by said body and a detachable cap comprising a base adapted to be seated over said cutter and engage the forward end thereof and also adapted to engage said abutment, and a palm rest pivotally connected adjacent one end to said base between its ends, a separately formed cam lever being pivotally carried by one of said parts in rear of the pivoted end of the palm rest and having a curved slot therein, and a pin being carried by the other of said parts and being seated in said curved slot whereby the movement of said palm rest relative to its base actuates said cam lever to clamp said cutter on its seat.
2. In a plane, in combination, a body provided with a cutter seat, a cutter positioned thereon, an abutment carried by said body and a detachable cap comprising a base adapted to be seated over said cutter and engage the forward end thereof and also adapted to engage said abutment, and a palm rest pivotally connected adjacent one end to said base between its ends, a separately formed cam lever being pivotally carried by one of said parts in rear of the pivoted end of the palm rest and having a curved slot therein, and a pin being carried by the other of said parts and being seated in said curved slot whereby the movement of said palm rest relative to its base actuates said cam lever to clamp said cutter on its seat, the end of said palm rest being provided with a shoulder adapted to engage said abutment upon such movement to thereby lock the cap against movement relative to the abutment and its plane body.
JAMES M. BURDICK.
CHRISTIAN BODMER.
Witnesses:
I. W. CHAPMAN,
W. J. WORAM.
Copies of this patent may be obtained for five cents each, by addressing the “Commissioner of Patents, Washington, D. C.”
_________________