No. 960,256 – Plane (Christian Bodmer) (1910)
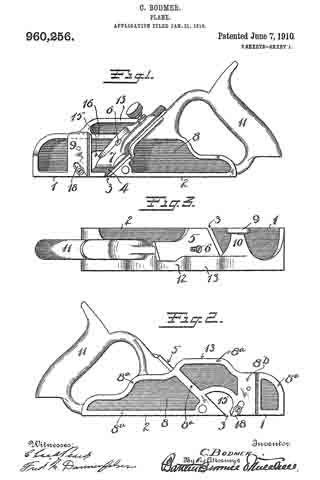
UNITED STATES PATENT OFFICE.
_________________
CHRISTIAN BODMER, OF NEW BRITAIN, CONNECTICUT, ASSIGNOR TO THE STANLEY RULE
& LEVEL COMPANY, OF NEW BRITAIN, CONNECTICUT, A CORPORATION OF CONNECTICUT.
PLANE.
_________________
960,256. Specification of Letters Patent. Patented June 7, 1910.
Application filed January 31, 1910. Serial No. 540,967.
_________________
To all whom it may concern:
Be it known that I, CHRISTIAN BODMER, a citizen of the United States, residing at New Britain, county of Hartford, State of Connecticut, have invented certain new and useful Improvements in Planes, of which the following is a full, clear, and exact description.
My invention relates to planes and particularly to that type of plane known as a fillister or rabbet plane.
The invention has particular reference to the construction of the plane body, my object being to overcome certain weaknesses that have heretofore existed in planes of this type.
In a fillister or rabbet plane, the cutting edge of the plane-iron is made the full width of the sole, or so that the side edges of the plane iron will be coincident with the sides of the plane, whereby the cut may be formed square up to each side edge or surface of the plane body. It follows that the throat or opening in the plane sole must therefore be the full width of the sole. This results in separating the sole transversely at a point intermediate its length, and places, therefore, the entire responsibility of holding the forward and rear sections of the sole in proper spaced relation upon the single side plate of the frame. It is at this point that heretofore has not only great weakness existed, but in the casting of the plane body great difliculty has been encountered in preventing warping and twisting of the parts, tending to throw the sections out of correct alinement and making the process of machining not only laborious but exceedingly difficult. By my improvement great strength is added at this point, warping and twisting during the process of casting are prevented, and machining is simplified and expedited. The plane body is made from cast iron and since this tool is usually a hand tool, it is obvious that it must be so constructed as to withstand severe usage. Heretofore planes of this type made from cast iron as in the present case have almost always been broken across the relatively narrow connection between the two sections of the plane. By my construction such a greater degree of strength is added that there is very little danger of breakage at any point even when the tool is roughly handled. The tool being a hand tool, it is obvious that great consideration must be attached to the element of weight, since unnecessary weight unduly taxes the strength of the workman. In this connection I have constructed a plane body so that the metal is economically disposed and well balanced throughout, my aim being to secure the highest degree of stability with a mininium amount of material.
In the accompanying drawings, Figure 1 is a side elevation of the complete plane, looking up from the left hand side. Fig. 2 is a view of the reverse or right hand side of the plane body. Fig. 3 is a plan view of Fig. 2. Fig. 4 is a relatively enlarged view showing a part of the plane in longitudinal section. Fig. 5 is a cross section of the plane on the line x–x. Fig, 6 is a cross section of the plane on the line y–y.
The plane body is cast in iron or steel and comprises the forward sole section 1 and the rear sole section 2, separated by a throat 3, in which the cutting edge of the plane-iron 4 stands when the plane is set up and adjusted ready for use.
5 is a seat for the plane-iron.
The throat 3 extends transversely and obliquely entirely across the plane body as best seen in Fig. 1, and it follows therefore, that the seat 5 not only inclines rearwardly but slants down toward one side of the plane. Any suitable mechanism may be employed for holding the plane-iron to the seat, such as the headed screw-stud 6 and the cap 7. The two sections 1–2. of the sole are integrally connected by a side plate 8 formed in this instance at the right hand side of the body, a part of the side plate bridging the throat 3 and being constructed, as hereinafter described, to afford great strength and to prevent warping and twisting. The plate 8 is provided with a raised bearing portion which is machined smooth, as indicated by the laterally offset ribs 8a–8a. These bearings 8a are raised with reference to the plain unfinished side of the said side plate 8, the area of said bearing portion being suflicient to afford a sufficiently long and broad seat, at the same time being much less than the entire area, thus simplifying exceedingly the operation of machining.
9 is an upwardly projecting bearing support at the opposite side (the left hand side) of the plane body, the same being in this instance parallel with the bearing portion of the side plate 8, and at right angles to the plane of the sole sections 1–2. This bearing-section 9 is connected integrally not only with the sole section 1, but also with the opposite side plate 8, said last connections being effected through the medium of the bridge rib 10.
11 is a handle preferably cast integrally with the plane body, but of course may be made capable of being connected to said plane body in any well known or desirable manner.
Referring particularly to the views 4–6, the connections between the throat and the rib sections of the plane will now be described. It is to be understood that the plane-iron, in this type of plane, is widest at its lower end, its middle and upper portion being narrowed down to clear the side plate 8. In the present instance, I avail myself of this feature to specially construct the bridge connection between the two sole sections, providing, where necessary, a solid strong mass of material and wherever possible a ribbed construction to secure the necessary strength and lightness. Immediately adjacent to the plane seat 5, where the side plate 8 leaves the rear section, I provide a relatively heavy mass of stock, as indicated at 12, Fig. 6. Immediately forward of this point, the bridge is arched up as indicated at 13, said arch descending at a point slightly forward of the plane of the throat and meeting the transverse bridge 10 which extends across to the opposite side-bearing or support 9. The lower part of the solid mass of material 12 near the lower end of the seat 5 is extended forwardly to form a curved rib 14, which performs the double function of a strengthening rib for the plane body and a deflector for the shavings, there being a clearance space 15 entirely through the plane body above the throat 3. This rib 14 curves forwardly and across the plane and meets the sole section 1 and the inner side of the support 9, being integrally formed with both of said parts. The arched portion 13 is provided with a recess or cavity 13a and between this recess or cavity 13a and the base of the rib 14 is a horizontally disposed strengthening rib 16, extending back to the heavy mass of material 12, and serving, together with the upper flange of the bridge 13 and the rib 14, to provide a connection between the sections 1–2 of maximum strength and minimum of weight. The inside of the plane body is of course hollowed out as at 17–17 to lighten the structure.
18–18 are scoring spurs or cutters employed on opposite sides of the plane to form score lines in advance of the plane-iron 4, said score lines being coincident with the opposite edges of said plane-iron.
The part 9 performs, in addition to the function of bearing for the adjacent side of the plane, the function of a support for a depth gage, such as is customarily employed in planes of this character. The opposite side (right hand side) plate is provided with a supporting portion 8b, upon which a depth gage may be adjustably supported. Since gages and other plane attachments are well known, no particular description is required herewith, it being merely proper to state that the part 8b performs not only the function of a bearing, but also a support for any attachment such as is customarily employed in tools of this character.
As has already been stated, my invention aims at producing a plane body of the type referred to which shall be accurately formed. One of the great difficulties to overcome I will now describe. It is a well known fact that the machining of the outer flat face of a casting releases the surface tension and permits the tension on the opposite (unmachined) face to act in such a manner as to twist and warp the structure; to illustrate, were it not for the recessed form of the outer face of the side plate 8, the machining of that side to produce a bearing surface would release the surface tension on the outer side and result in warping and buckling, tending to distort and throw out of line the two sole sections 1–2 of the plane body. This buckling would occur during or immediately following the machining process. To avoid this disastrous effect, I provide a construction which requires the machining of such a relatively small area of the surface 8 that the surface tension is not released to any dangerous extent. Consequently, the tension being substantially balanced on the opposite surface of the side plate 8, all tendency to injurious warping or twisting is eliminated. It should be stated that the unmachined held of surface metal between the bearing faces 8a of the side plate 8 affords more than a mere panel intended only for the reception of a name or number. In the present instance, this unmachined surface of substantial area is so located as to overcome the aforesaid injurious tendency of warping by reason of the lessening of the surface tension at the vulnerable point.
A further advantage growing out of this construction is the rapidity and ease with which this machining process may be effected. The sum of these advantages results in great economies that add to the durability or accuracy of the instrument.
While of course I have shown herein the preferred embodiment of my invention, it is obvious that in some respects the construction may be modified or varied without changing materially those features of improvement which characterize my invention. Hence it may be stated that I contemplate that reasonable latitude may be had in the particular design resorted to.
What I claim is:
1. A plane body formed of cast metal including two sole sections separated by a throat, a wall or plate integrally connecting said sections by an arch at one side of the plane body and including a plurality of substantially horizontally disposed and inwardly directed spaced ribs extending laterally across the plane body, a standard at the opposite side of the plane forming a bearing support projecting upwardly from the forward sole section and connected to the last mentioned rib, and still another rib extending across the plane body from the support on one side to the plate on the other side and forming a combined deflector and strengthening rib.
2. A plane body formed of cast metal including two sole sections separated by a throat, a wall or plate integrally connecting said sections by an arch at one side of the plane body and including a plurality of substantially horizontally disposed and inwardly directed spaced ribs extending laterally across said body, a standard at the opposite side of the plane forming a bearing support projecting upwardly from the forward sole section and connected to the last mentioned rib, and still another rib extending across said body from the support on one side to the plate on the other side and forming a combined deflector and strengthening rib, said last mentioned rib being also integrally connected with said bearing support and one of said sole sections.
3. A plane body formed of cast metal including two sole sections separated by a throat, a wall or plate at one side, connecting said sections by an arch at one side of the plane body, a standard at the opposite side of the plane forming a bearing support, the inner side of said standard being integrally connected to the inner side of said wall or plate, the outer or bearing side of said plate where said arch is formed having a relatively raised bearing surface, said bearing surface being machined, the relatively unraised portion being unmachined to balance surface tension on opposite sides of said plate at said arch.
4. A plane body formed of cast metal including two sole sections separated by a throat, a wall or plate connecting said sections at one side of the plane body and including a plurality of substantially horizontally disposed ribs at the inner side of said side plate, the outer or bearing side of said side plate having a relatively raised bearing surface, said bearing surface being machined, said unraised portion being unmachined, said unmachined surfaces being so disposed relatively to the forward and rear sections of the sole portions of the plane as to retain surface tension at the point where buckling would tend to occur between the two sole sections.
5. A plane body comprising a forward sole section and a rear sole section arranged in line and separated by a narrow throat, a wall or plate connecting said two sections at one side of the plane body, all of said parts being formed integrally by casting, the outer bearing surface of said wall or plate including a smoothed machined bearing surface and an umnachined surface arranged in a plane slightly below the plane of the bearing surface, said unmachined portion being so located with relation to the forward and rear sole sections as to retain surface tension at the point between the front and rear sole sections where buckling would tend to occur.
CHRISTIAN BODMER.
Witnesses:
THOMAS K. O’CONNOR,
JOSEPH M. HANCE.