No. 1,069,669 – Plane-Cap (Christian Bodmer And James M. Burdick) (1913)
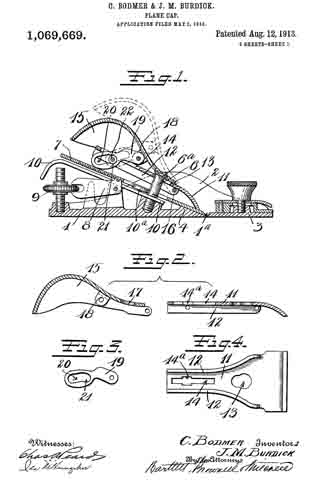
UNITED STATES PATENT OFFICE.
_________________
CHRISTIAN BODMER AND JAMES M. BURDICK, OF NEW BRITAIN, CONNECTICUT, ASSIGNORS TO THE
STANLEY RULE & LEVEL COMPANY, OF NEW BRITAIN, CONNECTICUT, A CORPORATION OF CONNECTICUT.
PLANE-CAP.
_________________
1,069,669. Specification of Letters Patent. Patented Aug. 12, 1913.
Application filed May 5, 1913. Serial No. 765,441.
_________________
To all whom it may concern:
Be it known that we, CHRISTIAN BODMER and JAMES M. BURDICK, citizens of the United States, residing at New Britain, county of Hartford, State of Connecticut, respectively, have invented certain new and useful Improvements in Plane-Caps, of which the following is a full, clear, and exact description.
This invention relates to improvements in the construction of planes and is more particularly concerned with cap pieces for the cutters or plane irons thereof of the type shown in our prior U. S. Patent No. 1,053,274, dated February 18, 1913.
The present invention aims to provide a cap piece of the general type shown in this prior patent, but embodying specific structural improvements.
A preferable embodiment of our improved form of cap piece is illustrated in the accompanying drawings in which —
Figure 1 is a longitudinal sectional view through a standard type of plane equipped with the cap piece of the present invention. Fig. 2 shows a longitudinal section through the palm rest and base sections, detached. Fig. 3 is a view in elevation of the cam lever. Fig. 4 is a bottom plan view of the base plate. Fig. 5 shows a side elevation, partly in section, of a modified form of cap piece, said cap piece being removed from the plane and the parts being shown in cutter clamping position. Fig. 6 is a longitudinal section of the palm rest section thereof, detached. Fig. 7 shows the base plate section thereof in longitudinal section and bottom plan. Fig. 8 is a detail of the clamping lever and its roller.
Referring to the drawings: numeral 1 designates the body of a plane of the channel type provided with side walls 2 and a detachable shoe 3 at the forward end thereof, the usual throat 1a being formed adjacent the forward end of the plane.
4 is a frog or seat for the forward end of the plane iron or cutter.
5 designates an interiorly threaded boss projecting upwardly from the plane body and carrying what is commonly termed a “cap screw” 6, provided with the usual headed end 6a. An adjusting lever 10 has its forward end seated over the boss 5 and is provided with an adjusting head 10a A second adjusting device is shown in the form of a lever member 8 pivotally mounted on the plane body and engaged at its rear end by an adjusting nut 9.
7 designates a plane iron or cutter provided with the usual longitudinal slot therein, this cutter being seated on the body of the plane with its forward end resting on the seat 4, and its cutting edge projecting into the throat 1a, the intermediate portions of the cutter resting respectively over the boss 5 and the end of the adjusting lever 8. The adjusting head 10a of lever 10 seats within the slot of the cutter. It will be, of course, understood that this slot is such as to enable the cutter to be seated on the plane body as described with the cap screw 6 projecting through the slot therein. We lay no claim to the specific structure of such a plane, inasmuch as it merely represents a standard type of plane with which the cap piece forming the subject matter of the present invention may be utilized. This cap piece embodies a base plate 11 having a curved forward end shaped to engage the forward end of the cutter resting on the seat 4, this base rearwardly of its curved end being provided with side flanges 12 preferably curving inwardly as seen in Fig. 4. Centrally of the base and intermediate the side flanges is a key-hole slot 13. Intermediate this lrey-hole slot and its rear end, this base plate is provided with a second and elongated slot 14 having lateral enlargements 14a intermediate its ends. Cooperating with this base member is a hollow convex cap 15 forming a palm rest, this palm rest section being hinged or pivoted to the base by means of a pivot pin 16 which may extend transversely of the base and through the side walls 12 at their forward ends. This palm rest section 15 is of sufficient width to inclose between its sides the rearwardly extending flanged portion of the base member 11, and in line with the narrow portion of the key-hole slot 13 thereof, is provided with an aperture 17 forming therewith an annular locking shoulder. 18 designates a bracket extending inwardly from the inner face of the palm rest section at a point in line with the forward end of the elongated slot 14 in the base member. To this bracket is pivotally secured the forward end of a clamping cam lever 19 which is provided with a cam slot 20 therein adjacent its rear or lower end, this cam slot having at its upper or forward end an angular offset forming a locking shoulder 21. This cam lever extends through the elongated slot 14 in the base and its end slot 20 guides upon a roller 22 journaled in the flanges 12 of the base and positioned within the lateral enlargement 14a of the elongated slot.
With the foregoing description in mind, it will be evident that in use, the plane cutter having been seated on the plane body in the desired position, the base 11 is brought to bring the enlarged end of its key-hole slot over the head 6a of the cap screw and is then moved upwardly to bring the head of the cap screw above the narrow portion of its key-hole slot, the palm rest section of the cap piece during this operation being held in the raised position indicated in dotted lines in Fig. 1. When this has been done, the palm rest section is then swung downwardly toward the base member 11, this movement causing the cam lever 19 to swing downwardly therewith to bring its lower edge into frictional clamping engagement with the upper face of the cutter (or of a clamping plate superposed thereon). This clamping action is effected through the cooperation of the cam slot 20 with the roller 22. When the palm rest section has been moved downwardly relative to the base sufficiently far to clamp the cutter on its seat, the roller 22 will have reached the upper or angularly offset end of the slot and will abut against the locking shoulder 21 formed thereby with the main body of the cam slot. At the same time, the aperture 17 at the forward end of the palm rest section will have been brought about the head ea of the cap screw. The edges of the palm rest adjacent said aperture being located at either side of said cap screw will prevent longitudinal movement of the entire cap piece relative to the cap screw and plane body with which it is rigid. The clamping engagement of the cam lever with the cutter is such that it holds the latter tightly on its seat, and under ordinary service conditions its position will be unchanged. The cutter, however, is always capable of being adjusted by the adjusting means provided without loosening the cap.
The frictional engagement of the cam lever with the cutter is maintained by reason of the engagement of the roller 22 with the locking shoulder 21 of the cam slot which shoulder serves to lock the cap piece in cutter clamping position and against accidental displacement. When it is necessary to detach the entire piece, however, a sharp pull on the palm rest section will move the shoulder 21 beyond the roller 22 and will permit the palm rest section to be raised, this action withdrawing the apertured forward end of the palm rest section from about the head of the cap screw so that the base may be moved relative to the cap screw to bring its head in alinement with the enlarged end of its key-hole slot 13, whereupon the base plate 11 and the attached palm rest section may be lifted from the plane body and from engagement with the cap screw.
In Figs 5 to 8, we have illustrated a modified form of cap piece embodying the same general idea. In Figs. 5 and 7, 11a designates the forward curved end of the base member, and 12a the side flanges thereof, the rear end of the base being preferably raised somewhat as at 13a and having formed in the forward end of its flange portion a key-hole slot 13b, and adjacent its rear end and rearwardly of said key-hole slot, an elongated slot 15a. A hollow convex palm rest section 16a is pivoted at its forward end to the flanges 12a and is provided at its forward end and at a point above the restricted end of the key-hole slot 15a with an aperture 17a providing the palm rest at that point with an annular locking shoulder. From the under face of the palm rest section adjacent the forward end of the slot 15a a bracket 18a extends inwardly. Complemental links 19a are pivoted to this bracket and extend through the elongated slot 15a in the base member. The flanges 12a adjacent their rear ends are provided with complemental alined cam slots 20a, these slots at their rear ends being provided with annular extensions or offsets forming locking shoulders 21a. The links 19a at their rear ends carry a clamping roller 22a whose spindle 23a guides in the cam slots 20a, the width of these slots corresponding substantially to the diameter of the spindle. The operation of this form is substantially the same as that of the first form of the cap piece described. The base member is seated on the cap screw and over the cutter in the same manner and the palm rest section is moved downwardly relative thereto, this movement moving the links 19a and their roller 22a downwardly, the cam slots 20a guiding the roller 22a into frictional clamping engagement with the upper face of the cutter and the spindles 23a of this roller seating at the end of its clamping roller in the offset extensions of these cam slots and engaging the locking shoulders to detachably lock the cap 6 in clamping frictional engagement with the cutter.
While we have herein illustrated preferable embodiments of the invention, it will, of course, be evident that the same is susceptible of modification in structure and relative arrangement of parts, within the spirit of the invention and the scope of the appended claims.
What we claim, therefore, and desire to secure by Letters Patent is :–
1. A cap piece for use in connection with plane bodies provided with abutment studs projecting upwardly from the cutter seats thereon, comprising a base adapted to be seated over a cutter, a palm rest pivotally secured to said base, a clamping lever carried by one of said parts, arranged upon movement of said palm rest relative to said base, to cooperate with means carried by the other of said parts to thereby clamp a cutter on its seat, said clamping means including a cam on one of said cooperating parts having a locking shoulder thereon, and a member carried by the other of said parts engaging said cam and arranged to engage said shoulder to lock said clamping lever in cutter clamping position.
2. A cap piece for use in connection with plane bodies provided with abutment studs projecting upwardly from the cutter seats thereon, comprising a base adapted to be seated over a cutter with its abutment stud projecting therethrough, a palm rest pivotally secured to said base and provided with a shoulder arranged to engage said stud upon relative movement of said palm rest and base, a clamping lever carried by one of said parts arranged, upon such relative movement, to cooperate with means carried by the other of said parts to thereby move said lever to clamp a cutter on its seat, said clamping means including a cam on one of said cooperating parts having a locking shoulder thereon, and a member carried by the other of said parts engaging said cam and arranged, upon such relative movement, to engage said shoulder whereby said clamping lever is detachably locked in cutter clamping position.
3. A cap piece for use in connection with plane bodies provided with abutment studs projecting upwardly from the cutter seats thereon, comprising a base adapted to be seated over a cutter, a palm rest pivotally secured to said base, a clamping lever pivotally carried by said palm rest and guiding on said base, a cam slot formed in one of said parts, said slot having an offset therein forming a locking shoulder, and a stud carried by the other of said parts engaging in said cam slot and arranged upon movement of said palm rest relative to said base, to move said clamping lever into frictional clamping engagement with a plane cutter, said stud at the end of such clamping movement, being positioned within said slot offset and against said shoulder to thereby detachably lock said parts in counter clamping position.
4. A cap piece for use in connection with plane bodies provided with abutment studs projecting upwardly from the cutter seats thereon, comprising a base adapted to be seated over a cutter with its abutment stud projecting therethrough, a palm rest pivotally secured to said base and provided with a shoulder arranged to engage said stud upon relative movement of said palm rest and base, a clamping lever pivotally carried by said palm rest and guiding on said base, and arranged, upon such relative movement of the parts, to cooperate with means carried by said base to clamp a cutter on its seat, said clamping means including a cam slot formed in one of said parts and having an offset thereon providing a locking shoulder or abutment, and a stud carried by the other of said parts engaging in said cam slot and arranged, upon movement of said palm rest relative to said base, to move said clamping lever into frictional clamping engagement with a plane cutter, said stud engaging with said shoulder or abutment at the end of such relative movement, to detachably lock said clamping lever in cutter clamping position.
CHRISTIAN BODMER.
JAMES M. BURDICK.
Witnesses:
ALBERT W. RITTER,
PHILIP B. STANLEY.
Copies of this patent may be obtained for five cents each, by addressing the “Commissioner of Patents, Washington, D. C.”
_________________