No. 37,694 – Improvement In Bench Planes (Seth C. Howes) (1863)
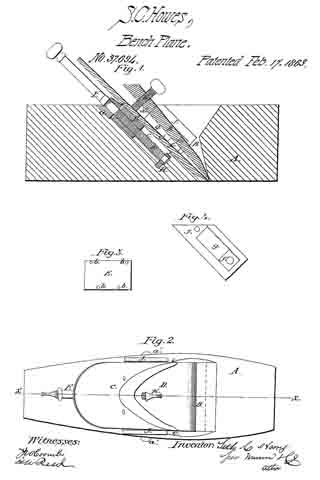
UNITED STATES PATENT OFFICE.
_________________
SETH C. HOWES, OF SOUTH CHATHAM, MASSACHUSETTS.
IMPROVEMENT IN BENCH-PLANES.
_________________
Specification of Letters Patent No. 37,694, dated February 17, 1863.
_________________
To all whom it may concern:
Be it known that I, SETH C. HOWES, of South Chatham, in the county of Barnstable and State of Massachusetts, have invented a new and useful Improvement in Bench-Planes, such as are used by joiners and other artisans in wood; and I do hereby declare that the following is a full, clear, and exact description of the same, reference being had to the accompanying drawings, making part of this specification, in which —
Figure 1 is a vertical section of my invention, taken in the line x, x, Fig. 2. Fig. 2 is a plan or top view of the same. Figs. 3 and 4 are detached views of parts pertaining to the same.
Similar letters of reference indicate corresponding parts in the several figures.
This invention relates to an improvement in that class of planes which are commonly termed “bench-planes,” comprising the fore-plane, smoothing-plane, jack-plane, jointer, &c.
The invention consists in a novel and improved mode of adjusting the plane-iron to regulate the depth of the cut of the same, in connection with an adjustable cap, all being constructed and arranged in such a manner that the plane-iron may be “set” with the greatest facility and firmly retained in position by the adjustment simply of the cap to the plane-iron, after the latter is set, and the cap also rendered capable of being adjusted to compensate for the wear of the “sole” or face of the plane-stock.
To enable those skilled in the art to fully understand and construct my invention, I will proceed to describe it.
A represents the stock of the plane, which may be constructed of wood, as usual, and B is the throat or opening in the stock, in which the plane-iron C and cap D are fitted. The iron C is of the usual shape, and it has four holes made in its back surface, to receive a corresponding number of spurs, b, which are on the front side of a square nut, E, the latter being fitted in an inclined recess, c, in the stock, at the back part of the throat B.
F is a rod, the lower portion of which has a screw, d, cut on it. On this screw d the nut E is fitted. The rod F, just above the screw d, is fitted in a socket or bearing, G, in the upper part of the stock. The lower end of the rod F is fitted in a bearing, H. (See Fig. 1.)
D represents the cap, the lower end of which presses against the front side of the plane-iron G, when the plane is in condition for use. The cap D is provided with pins or trunnions e e — one at each side — and these pins or trunnions are fitted in bearings f f, which are of square or rectangular form, and fitted in oblong slots g g in metal plates J J, the latter being secured in an inclined position in the stock A — one at each side of the throat B — by means of screws a’. The bearings f at one side are notched or serrated, and the upper sides of the slots g are also serrated, so that the serrated edges of the bearings may engage therewith. (See Fig. 4.) By this arrangement the bearings are prevented from casually moving in their slots g. Through the upper part of the cap D a screw, K, passes, and this screw bears against the plane-iron C and keeps the spurs b of the nut E engaged with the holes in the plane-iron, and the plane-iron in close contact with the nut, as will be fully understood by referring to Fig. 1. In order to adjust or set the plane-iron C, the rod F is turned, the plane-iron being thereby raised and lowered, the screw K being turned so as to relieve the plane-iron C of its pressure as well as of the pressure of the lower end of the cap D. When the plane-iron is set, the screw K is turned so as to press the lower end of the cap D against the lower part of the plane-iron, and by this adjustment the pressure of the screw K keeps the plane-iron in contact with the nut E. The plane-iron, therefore, it will be seen, is firmly retained in position when the plane is in condition for use. In case the sole or face of the stock A becomes worn by use, or requires to be faced or planed off, the cap is elevated by removing the plates J J from the stock and placing the bearings f f rather higher in the slots g g, the serrated edges of the bearings and slots holding the bearings in proper position at any desired points in the slots.
Having thus described my invention, what I claim as new, and desire to secure by Letters Patent, is —
The rod F, having the screw d cut upon it, and provided with the nut E, with spurs b on its outer surface, to fit in holes in the plane-iron C, in combination with the cap D, provided with the screw K and trunniouse e the f f, which are placed in slotted plates J J , and retained therein at the desired point by the serrated edges of the bearings and the slots or a equivalent means, all arranged substantially as set forth.
SETH C. HOWES.
Witnesses:
JOHN G. DOANE,
FREEMAN E. CHASE.