No. 898,556 – Mortising-Plane (Maurice A. Clark) (1908)
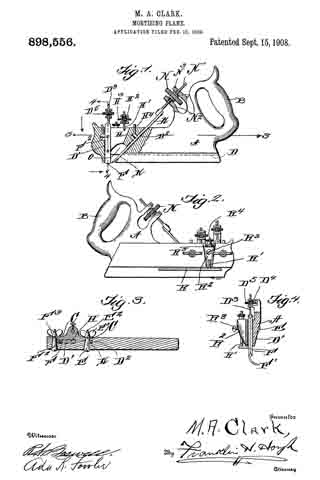
UNITED STATES PATENT OFFICE.
_________________
MAURICE A. CLARKE, OF EDMONTON, ALBERTA, CANADA.
MORTISING-PLANE.
_________________
898,556. Specification of Letters Patent. Patented Sept. 15, 1908.
Application filed February 15, 1908. Serial No. 416,095.
_________________
To all whom it may concern:
Be it known that I, MAURICE A. CLARK, a subject of Great Britain, residing at Edmonton, in the Province of Alberta, Dominion of Canada, have invented certain new and useful Improvements in Mortising-Planes; and I do hereby declare the following to be a full, clear, and exact description of the invention, such as will enable others skilled in the art to which it appertains to make and use the same, reference being had to the accompanying drawings, and to the letters and figures of reference marked thereon, which form a part of this specification.
This invention relates to new and useful improvements in planes and the object in view is to produce a simple and efficient device of this nature designed especially for cutting mortises for the reception of stairs and consists essentially in the provision of two cutting blades beveled upon their inner edges and placed side by side in advance of an obliquely positioned plane or blade, the parts of the apparatus being so adjusted that a groove of varying depth may be cut.
The invention comprises various details of construction and combinations and arrangements of parts which will be hereinafter fully described and then specifically defined in the appended claims.
I illustrate my invention in the accompanying drawings, in which:–
Figure 1 is a side elevation of the plane, parts being shown in section. Fig. 2 is a side elevation, Fig. 3 is a cross sectional view and Fig. 4 is a sectional view taken on line 4–4 of Fig. 1.
Reference now being had to the details of the drawings by letter, A designates a stock of the plane, made preferably of metal, and has an integral handle B at one end thereof. Said stock has a vertically formed slot D’ therein for the reception of the cutting blades F, details in edge view of which are shown in Fig. 4 of the drawings. It will be noted upon reference to said blades F, that each of said blades is beveled and is designed to cut two slots spaced apart and parallel to each other. Said blades are mounted upon a screw D3 which passes through the arms of the bracket extension D4, as shown in Fig. 4 of the drawings, and D5 is a wheel with a milled edge and having a threaded aperture to engage the ends of said screws D3 whereby as the screw is raised and lowered, the depth at which it may be desired to have the blades cut, may be regulated. In order to hold the blades securely, a tapering pin F2 is provided passing through a similar shaped transverse aperture, as shown in Fig. 3 of the drawings the marginal edge of said pin being adapted to be drawn against the edges of the two blades F by means of a thumb nut F3 upon a tmeaded end of said pin.
H designates a wedged block which is mounted in a vertical slot in the stock and H’ designates a pin which is fastened to said wedged block and extends through the bracket arms H2 similar in construction to the bracket arms shown in Fig. 4 of the drawings and H3 is a wheel having a threaded opening for engagement with the screw H’, whereby said block may be raised or lowered.
It will be noted that the block H cooperates with the tapering pin F2 for the purpose of frictionally holding the blades in adjusted positions.
K designates a knife which is mounted in a diagonally disposed slot D2 formed in the stock and E designates a pin which is tapered, provided with a threaded end E2 upon which a thumb nut E3 is mounted, said pin E passing through a tapering aperture in the stock plane.
H4 designates a set screw mounted in a threaded aperture in the stock and adapted to bear against the pin E to hold the same in an adjusted position. A suitable screw N2 is fixed to the knife K, said screw not passing through the bracket arms N3 of the stock and N is a wheel having a threaded aperture to iit the screw end N’ and provided with a milled circumference.
R designates a gage having an integral rod R’ projecting therefrom and extending through an aperture in a projecting portion R2 of the stock, which projecting portion carries a set screw R3 for engagement with the rod R’ to hold the same m an adjusted position. The upper end of said rod R’ is threaded to receive an adjusting wheel R4 with a milled edge, and R5 designates a projection upon said wheel R4 which is swiveled in a recess in said projection R2.
In operation, the cutting blades F being adjusted with their cutting ends projecting below the bottom of the plane, the apparatus is positioned over the surface to be cut, the two blades F cutting the marginal edges of the groove while the planer or plowing blade K follows on and mortises out the parts intermediate the side walls of the groove. Owing to the adjustment of the gage R upon the stock, it will be noted that the depth at which it may be desired to mortise may be readily adjusted by simply loosening the set screws and raising or lowering the gage R after which the screws may be tightened and the apparatus held in its adjusted position.
by the provision of a mortising plane as shown and described, it will be observed that means is afforded whereby a groove or channel may be readily formed without inconvenience, even though the rnortising to be done may be in positions ordinarily inaccessible by means of the usual planes provided for the purpose and so arranged that the blades may be readily adjusted for mortising at different depths.
What I claim is :–
1. A mortising plane comprising a stock having a vertical slot in the forward end thereof, an inclined planer blade, blades mounted in said slot with their inner faces in contact with each other, a pin passing through a ertures in said blade, a screw to which said pin is secured, a bracket arm rising from the stock and having laterally extending fingers which are spaced apart and provided with apertures, a wheel mounted between said fingers and provided with a central threaded aperture through which said screw passes, a wedge block mounted in said slot and bearing against corresponding edges of said blades, means for moving said block, a screw having an unthreaded tapering portion passing through the stock and adapted to bear against the edges of said blades opposite said wedge block, and a nut upon said blade engaging stock, as set forth.
2. A mortising plane comprising a stock having a vertical slot in the forward end thereof, an inclined planer blade, blades mounted in said slot with their inner faces in contact with each other, a pin passing through apertures in said blade, a screw to which said pin is secured, a bracket arm rising from the stock and having laterally extending fingers which are spaced apart and provided with apertures, a wheel mounted etween said fingers and provided with a central threaded aperture through which said screw passes, a wedge block mounted in said slot and bearing against corresponding edges of said blades, a second bracket arm rising from the stock and having laterally projecting fingers which are spaced apart, a screw fastened to the block and passing through the apertures in the adjacent fingers, means for raising and lowering the stock connected to the block, and a screw passing through a transverse aperture in the stock and provided with an unthreaded tapering portion bearing against the edges of said blades, as set forth.
In testimony whereof I hereunto affix my signature in the presence of two witnesses.
MAURICE A. CLARK.
Witnesses:
HENRY GILBERT,
WILLIAM CHARLES CUNNINGHAM.