No. 752,365 – Spokeshave (John H. Spear) (1904)
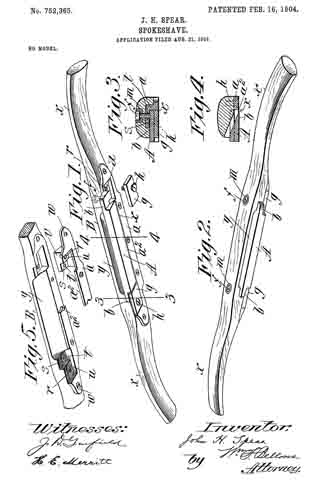
UNITED STATES PATENT OFFICE.
_________________
JOHN H. SPEAR, OF SPRINGFIELD, MASSACHUSETTS.
SPOKESHAVE.
_________________
SPECIFICATION forming part of Letters Patent No. 752,365, dated February 16, 1904.
Application filed August 21, 1903. Serial No. 170,298. (No model.)
_________________
To all whom it may concern:
Be it known that I, JOHN H. SPEAR, a citizen of the United States of America, and a resident of Springheld, in the county of Hampden and State of Massachusetts, have invented certain new and useful Improvements in Spoke-shaves, of which the following is a full, clear, and exact description.
This invention relates to improvements in spokeshaves, and more particularly pertains to the means for securing the adjustment convenintly of the blade or knife so that it will cut a fine or thick shaving, as desired, and for confining the knife when adjusted.
The invention consists in a spokeshave constructed substantially as shown in the accompanying drawings and as set forth in the claims.
In the drawings, Figure 1 is a perspective view of the improved spokeshave as seen at its under or shaving side. Fig. 2 is a perspective view of the same as seen looking at the back and top thereof. Fig. 3 is a cross-sectional view as taken on the line 3 3, Fig.1. Fig. 4 is a cross-sectional view as taken on the line 4 4, Fig. 1. Fig. 5 is a perspective view of the under side of the stock or body of the spokeshave, showing also a metallic fitting therefor, a right-hand half of the latter being indicated as broken away and removed from its place of application on, and within, the stock, which is shown recessed for the reception thereof.
Similar characters of reference indicate corresponding parts in all of the views.
Referring to the drawings, A represents the knife or blade, and B the body or stock, having handles x x at its opposite ends, as usual, the said stock being intermediately provided with the usual throat-forming recess y and has a metallic fitting a, adapted to be inset into suitably-formed recesses in the stock therefor and to overlap the under or working-face side thereof and to constitute by its straight-edged portion a2 one boundary of the throat, adjacent which, more or less closely thereto, is the cutting edge x of the blade a. The said fitting a is preferably made as a metallic casting having, as shown in Figs. 1 and 5, ear-lugs w at its ends by which to screw it to the stock, and its inset portion v is formed step-shaped at each end, the one step s at the innermost plane having a tapped perforation t therethrough for the screw f penetrating from the front or upper side of the stock, which has its end in bearing against the inner face of the end lug b of the blade, and the more outwardly-disposed step u has a perforation r, which is screw-tapped, receiving therein the screw h for holding the clamping-plate g against the outer face of the end lug b of the blade.
The parts are originally constructed and relatively arranged so that when the inner face of the end lugs of the blade are practically in contact with the face of the inner step s the cutting edge x of the blade will not be outwardly beyond the under face of the throat-plate.
By loosening the screws h for the clamping-plates g the blade, with its end lugs b b, may of course be crowded bodily transversely and outwardly beyond the plane of the throat-plate, and this is done by inscrewing the screws f f, which penetrate through and beyond the face of the step s of the aforesaid metallic fitting, whereupon the screws h h are set again to confine the clamping-plates to hold the blade-lugs firmly in their adjusted positions as crowded by and in contact on the inner ends of the adjusting-screws f f. The said screws may by having their positions of contact, as indicated in Fig. 3, well toward the inner edges of the blade-lugs b b impart to the blade somewhat of a rocking movement for adjustment, or it may be a bodily-displacing action, the effect being to either swing the blade on a longitudinal axis back from the cutting edge to bring the location of the cutting edge more or less outward for the desired rankness of cut or to displace the blade outwardly without changing the direction of its plane for acquiring practically the same condition for any desired character of shaving.
Inasmuch as the adjusting-screws f f are repeatedly rotated either inwardly or outwardly for varying the rankness of the cut to be taken or made by the knife, and in order that the wood from which the stock of the tool is composed may not be gouged out by the screw-driver, annular cup-shaped and centrally internally perforated bushings m are inset into circular sockets within the upper sides of the stock, it being of course understood, however, that the threaded shanks of the screws f acquire their screw-threaded engagements in and through the portions of the metallic fitting, the inner sides of which constitute the aforesaid innermost steps s s.
This spokeshave may not only be most readily adjusted for any manner of shaving required, but the knife may be bodily transversely adjusted to give any desired width of throat-opening and to correspond with the wearing away at the cutting edge of the knife.
Having thus described my invention, what I claim, and desire to secure by Letters Patent, is —
1. In a spokeshave, the combination with the stock having a throat-recess and having step-formed supports endwise outside thereof, of the knife having end lugs adjacent the innermost steps, the clamping-plates adjacent the outermost steps and overlapping the lugs of the knife, the screws h h for confining the clamping-plates and the adjusting-screws engaging through the aforesaid innermost steps and contacting against the inner faces of the knife-lugs, for the purposes set forth.
2. In a spokeshave, the combination with the stock having the throat-recess and the metallic throat-plate constructed with the stepped portions s and u, let into the body of the stock and having the screw-holes t and r, of the knife a having the end lugs b b the inner faces of which are arranged adjacent the faces of the steps s s, the adjusting-screws f f penetrating said stepped portions s s from the front of the stock and having their inner ends in engagement against the inner faces of the lugs, the clamping-plates g g facewise adjacent the steps u u and overlapping the outer faces of the lugs, and the clamping-screws h h, substantially as described.
3. In a spokeshave, in combination, the stock having the throat-recess and having the inset throat-plate provided with the end portions constructed with the steps s and u, the knife having the end lugs, the adjusting-screws and the bushings m, arranged relatively to the headed portions of said screws in sockets in the top of the stock, the clamping-plates g g and the confining-screws h h therefor, arranged as shown.
Signed by me at Springfield, Massachusetts, in presence of two subscribing witnesses.
JOHN H. SPEAR.
Witnesses:
WM. S. BELLOWS,
A. V. LEAHY.